Being a high-performance lathe the MAXXTURN 45 is a perfect solution for economic complete machining. It has just the right features to guarantee significant increases in productivity. Highly dynamic drive systems help to achieve this. The pleasant side effect: the required precision and rigidity for the production of complex turned and milled parts are also ensured.
The MAXXTURN family in the meantime comprises five members: the MAXXTURN 25, 45, 65, 95 and 110. While the smaller three high-performance universal lathes with their counter spindle represent the perfect solution for the economic complete machining of barstock and chuck parts, the MAXXTURN 95 and 110 concentrate on the machining of shafts and flange parts. Fitted with a Y axis, driven tools, a high-precision C axis and very high rapid-motion speeds, the MAXXTURN series offers everything the customer desires, to not only manufacture complex machined parts in high quality, but also cost-effectively.
Extensive range of parts
Depending on the make, the MAXXTURN 45 forms the basis for efficient machining of precision and machined parts. The range of manufactured workpieces ranges from hydraulic/pneumatic components, to machines as well as engine and automotive parts, all the way to components from the field of biomedical engineering or the fields of materials and bulk material handling. Friction and antifriction bearing parts are just a few more examples of the nearly endless possibilities.
Tailored automation
A swing loader is included for automatic loading and feeding out of the machined parts. This extremely compact and integrated loader is controlled via the machine control. The exceptional combination of a swivel movement and a linear movement, driven by servomotors, guarantees simple and fast setup. As a result, preformed raw parts can also be inserted position-oriented into the clamping device. After machining has been completed the finished parts are transported out of the machine via the parts catcher.
EMCO has two different versions of bar loaders on offer for bar work: The swing loader as a universal loading system for all types of preformed blanks and the short bar loader SL1200 as the perfect solution for automatic feeding and loading of cut-to-length bars.
The highlights of the MAXXTURN series
One of the characteristics which distinguishes the entire MAXXTURN line is that the Y axis is integrated in the body of the machine. This ensures maximum stability, as well as utmost precision of all parts manufactured. The extremely wide distances between the guides make for stable turning and offer the operator additional possibilities for complete machining.
The compact counter spindle is an additional highlight, taking over workpieces position-oriented and with utmost precision for machining the reverse side. This avoids having to clamp workpieces a second time, thereby avoiding wait time, which in turn increases productivity and makes for shorter part delivery periods.
The tool turret with single-motor engineering offers space for 12 VDI25 tool holders. Each station can accept driven tools. A servo motor powers the driven tools and the swivel movement, respectively. The tool holders, equipped with EMCO joggling plates, allow easy tool insertion with repeatable accuracy without the need for
time-consuming adjustments.
In the course of modular assembly customers can choose between a SIEMENS (incl. ShopTurn dialogue interface) and a FANUC control interface (incl. Manual-Guide-i control interface).
Technical Details / The MAXXTURN Machine Concept
Machine base
The 72° inclined bed is the core of the machine. The very rigid and compact welded-steel construction provides an extremely solid basis for a precise as well as economic production. The advantages of steel, in comparison to machine casting, are on the one hand its higher rigidity and on the other hand the superior thermal behavior of the lathes during warm-up. For optimum damping of the vibrations and resonances which naturally occur during machining, the machine base of the MAXXTURN 45 is filled with special vibration-damping material. A perfect turning finish and true running accuracy are the result. Reinforcing materials provide additional rigidity in zones that are often subject to intense stress.
The MAXXTURN 45 is equipped with roller guides which are free from wear and bedded without play. They are delivered with highest possible pre-stress and are bolted onto high-precision, ground bearing pads. Perfect guidance qualities without any stick-slip effect guarantee best surface qualities for all machined parts. Covers along the guides, as well as additional telescope covers made of stainless steel increase operational safety and durability.
Main spindle
The high driving power of the spindle combined with optimal torque curve ensures economic efficiency in cutting steel, as well as high-speed cutting of aluminum. The main spindle guarantees a bar capacity of up to 45 mm and is supported with extra large precision bearings. These allow for a wide range of speeds with extremely good running truth. A symmetrical headstock with fitted cooling fins ensures optimum thermostability.
Tailstock
On the MAXXTURN 45 with tailstock, the tailstock is set up on the linear roller slide and can be positioned automatically within a range of 510 mm. The rolling centre with MK4 shaft is directly integrated into the tailstock and can be removed using a pressure wedge.
Counter spindle
On the MAXXTURN 45 S, which is equipped with a counter spindle, the counter spindle headstock is placed on a separate linear roller slide and can be positioned within a range of 510 mm. A stroke-monitored parts ejector, flushed with coolant, ensures safe removal of the finished parts.
Tool holder
The tool holder consists of a 12-position VDI25 radial turret with single-motor engineering and quick-change system. All 12 stations can accept driven tool holders. A servo motor powers the driven tools and the swivel movement, respectively. The machine operator may adjust the slewing speed at any time, using a feed-override switch. The turret can be used on both spindles and switches with direction logic. This means that it always takes the shortest way when swiveling to the next tool. The tool holders, equipped with the EMCO joggling plate and DIN 5480 coupling, allow easy tool insertion with repeatable accuracy without time-consuming adjustments.
C axis / main spindle (model-specific)
The C axis is part of the machine’s standard equipment. The spindle can be positioned with a resolution of 0.001°. A directly attached no-contact rotary encoder without a belt drive guarantees the precision of the C axis as well as precise contour milling. In addition, the main spindle can be clipped into the right position for drilling and milling operations using a spindle brake.
Y axis (model-specific)
The Y axis is integrated in the standard build of the machine and is positioned at an angle of 90° in relation to the X axis. Extremely short protruding lengths are the basis for solid lathing and drilling operations, as well as for milling without receiving imprecise contours.
Feed drive
Highly dynamic three-phase drives in all linear axes, with preloaded circulating ball spindles, provide high feed forces and positioning with repeatable accuracy.
Measure system
Incremental measure systems in the feed motor are integrated in all linear axes.
Clamping unit
The clamping unit is a hydraulic clamping system with a bar capacity of up to ø 45 mm, including a programmable chuck stroke monitor and direct measure system. Time-consuming adjustments with the tools are thereby substituted by a simple training in Teach-In-Mode.
Lubrication
The MAXXTURN 45 uses an automatic centralized lubrication system with lubricant-saving impulse lubrication due to its integrated pressure and quantity monitoring.
Coolant device
A central coolant supply through the VDI interface at the turret and through the tool holder ensures optimal cooling and lubrication during the machining process. An additional coolant pipe has been installed to clean the clamping devices and the work area.
Hydraulic system
The hydraulic system is a high-pressure compact hydraulic system with a pump and a fine filter in the head pipe, with which the chucking pressure can be more finely adjusted, which is an absolut must for clamping sensitive work-pieces in the main and the counter spindle. Thanks to its compact construction it only has a small footprint.
Casing
The casing of the machine is completely closed. Its door is monitored with safety switches to prevent operator injury and features a sizeable viewing window made of laminated safety glass.
Finished parts pick-up unit (optional)
The pneumatically operated pick-up unit removes finished parts from the main or the counter spindle. The parts are gently transported into a finished parts container outside of the work area. Max. length of finished parts: 120 mm; max. ø 45 mm; Max. weight:
2 kg
EMCONNECT
A digital process assistant for the comprehensive integration of customer- and system-specific applications for controlling the machine and the production flow, EMCONNECT interlinks and networks the production environment. In order to create more efficient work processes without losing sight of the machines’ outstanding reliability in all operating modes, the operating sequences focus on the user and their requirements.
With EMCONNECT, users can access important additional features directly via the control panel, which means that it is possible to access all important details, data and systems directly and centrally at the machine. EMCO’s modular system makes it possible to implement even project- and customer-specific applications in an extraordinarily flexible way. Thus, EMCONNECT is the key to ideal work processes and increased productivity.
The range of available apps is continuously being expanded. As of now, for example, you may download our Option Shopfloor Data for the collection of machine and operating data. It ensures comprehensive monitoring of all machines as well as process organisation in the production area. This product is characterised especially by machine and manufacture independence and mobile access to the machine state using a smartphone or tablet PC.
In order to minimise machine downtimes, we are currently developing the EMCONNECT Data Service for targeted preventive maintenance. We will be happy to show you a first version of this application at our booth.
Technical DataMAXXTURN 45Max. bar capacity [mm] Ø 45 (optional: Ø 51)
Max. speed [rpm]
Main spindle 0 – 7000
Counter spindle 0 – 7000
Driven tools 0 – 8000
Max. Drive power [kW]
Main spindle / counter spindle (Counter Spindle or Fanuc) 15 / 15
Max. Traverse path [mm]
X 160
Y +40 / -30
Z 510
Rapid speed X/Y/Z [m/min] 24 / 10 / 30
Number of tool adapters 12 x VDI 25
Number of tool positions 12 Models:
• Choice of control: Fanuc or Siemens
• MT 45 MY: Tailstock version with driven tools and Y axis
• MT 45 S: Counter spindle version without driven tools
• MT 45 SM: Counter spindle version with driven tools
• MT 45 SMY: Counter spindle version with driven tools and Y axis
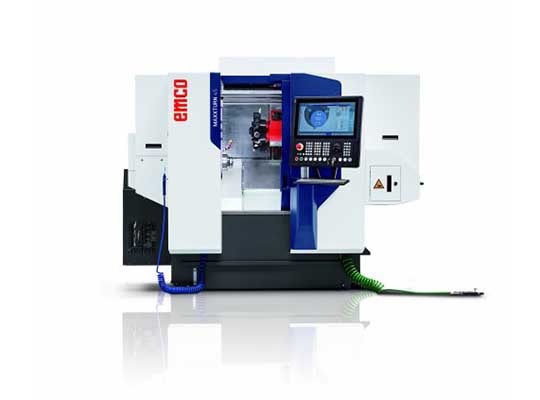
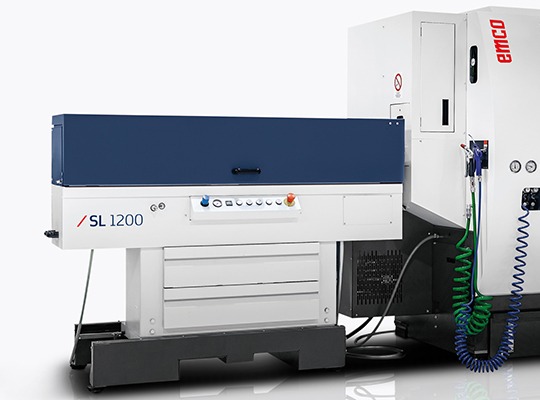
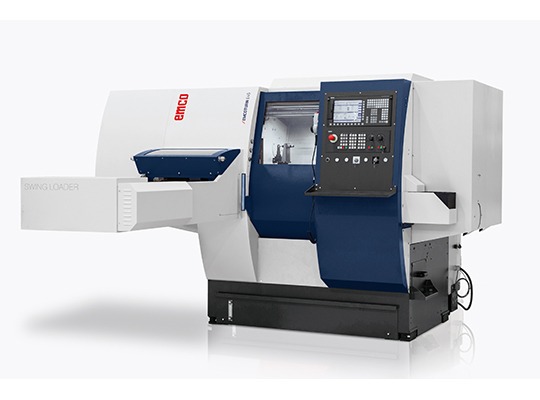
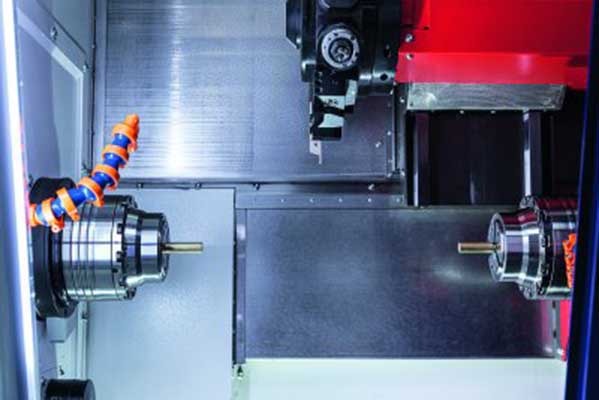
Further information can be found online at www.emco-world.com